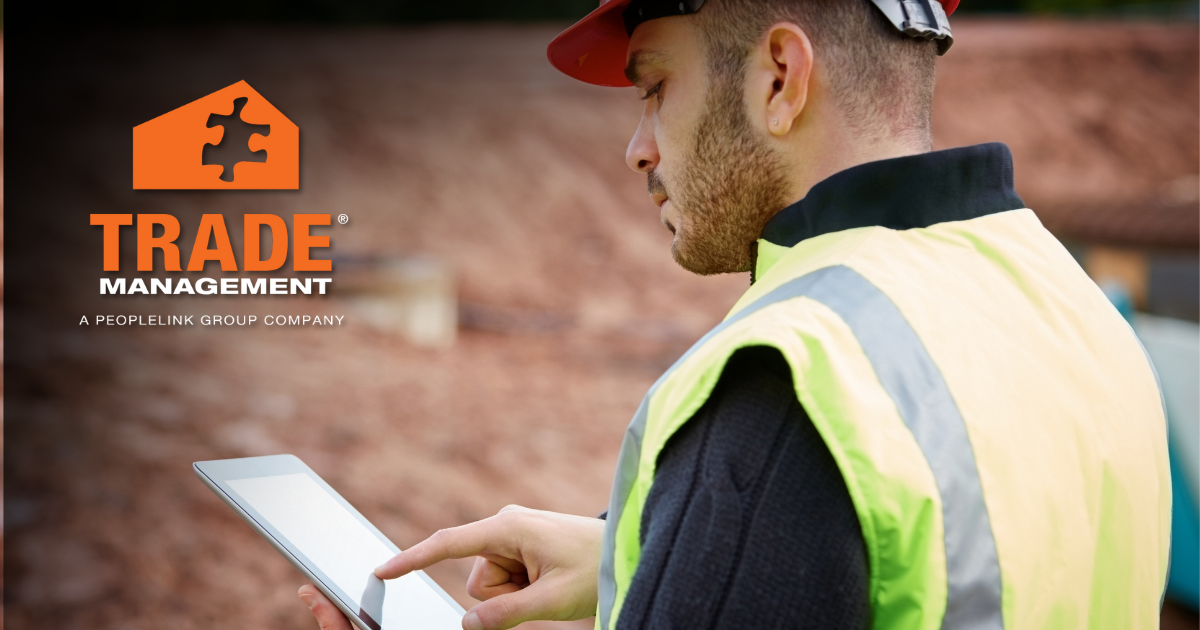
The skilled trades industry, often seen as rooted in traditions, is undergoing a significant transformation. From construction and welding to HVAC and plumbing, the integration of modern technology is changing how trade professionals work. As automation, smart tools, and advanced software enter the stage, skilled trades are evolving into tech-enabled careers. For employers and tradespeople alike, understanding these changes is critical. Let’s review recent technological developments in the skilled trades and the resulting benefits.
Automation is making waves in fields like manufacturing, electrical work, and construction. An increasing percentage of industry professionals, 46%, plan to utilize more digital tools in their day-to-day operations going forward. Robotic welding arms, automated cutting machines, and 3D printing are now common in many environments. Such automation can reduce human error, enhance productivity, and make repetitive or hazardous tasks safer. Skilled trades professionals are now working with machines, not facing replacement by them.
Smart tools equipped with sensors and Bluetooth connectivity are becoming standard. Think of digital torque wrenches, smart HVAC gauges, and connected diagnostic equipment. IoT (Internet of Things) devices provide real-time data and analytics to boost performance. For example, HVAC technicians can now use smart thermostats and sensors to remotely monitor system performance and troubleshoot issues before stepping onsite. Smart tools allow for streamlined workflows, predictive maintenance, and increased client satisfaction through faster service.
Augmented reality (AR) and virtual reality (VR) are revolutionizing training in the skilled trades. In fact, studies indicate 73% of skilled trades training programs are incorporating technology. Trainees can now experience lifelike simulations without the risks or costs associated with live training environments. As a result, trainees complete onboarding more quickly and with reduced training-related injuries and improved knowledge retention. Skilled tradespeople can also upskill more easily, staying ahead in a fast-changing field.
Staffing, scheduling, compliance, and payroll are easier than ever thanks to platforms designed specifically for trade-based businesses. Digital workforce management tools optimize crew assignments and track job performance in real time. Using digital workforce management tools results in better resource allocation, real-time job visibility, and easier compliance and reporting. For staffing agencies and employers alike, these tools mean less admin work and more focus on outcomes.
One of the most promising aspects of increasing technology in skilled trades is its power to attract a younger generation of workers. As digital natives, Gen Z and Millennials are attracted to careers that incorporate modern tools, smart devices, and innovative tech. In fact, a recent survey found that 31% of respondents believe technology can drive industry growth by making skilled trades more appealing to younger workers. From using AR/VR for immersive training to working with connected diagnostic tools and automation systems, the tech-driven nature of today’s trades aligns well with the interests and skillsets of younger job seekers. By modernizing how trade work is performed and taught, the industry is not only improving efficiency but also securing its future workforce.
Technology in skilled trades is here to stay. For companies and professionals who embrace it, the opportunities are enormous, from safer job sites to higher productivity and better training. Partner with a skilled trades staffing agency that understands both your workforce needs and the technology driving the industry forward. Contact Trade Management today for a free consultation!